Table of Contents
Categories
Electroplated Linear Bearing: 8 Factors for Guaranteed Reliability
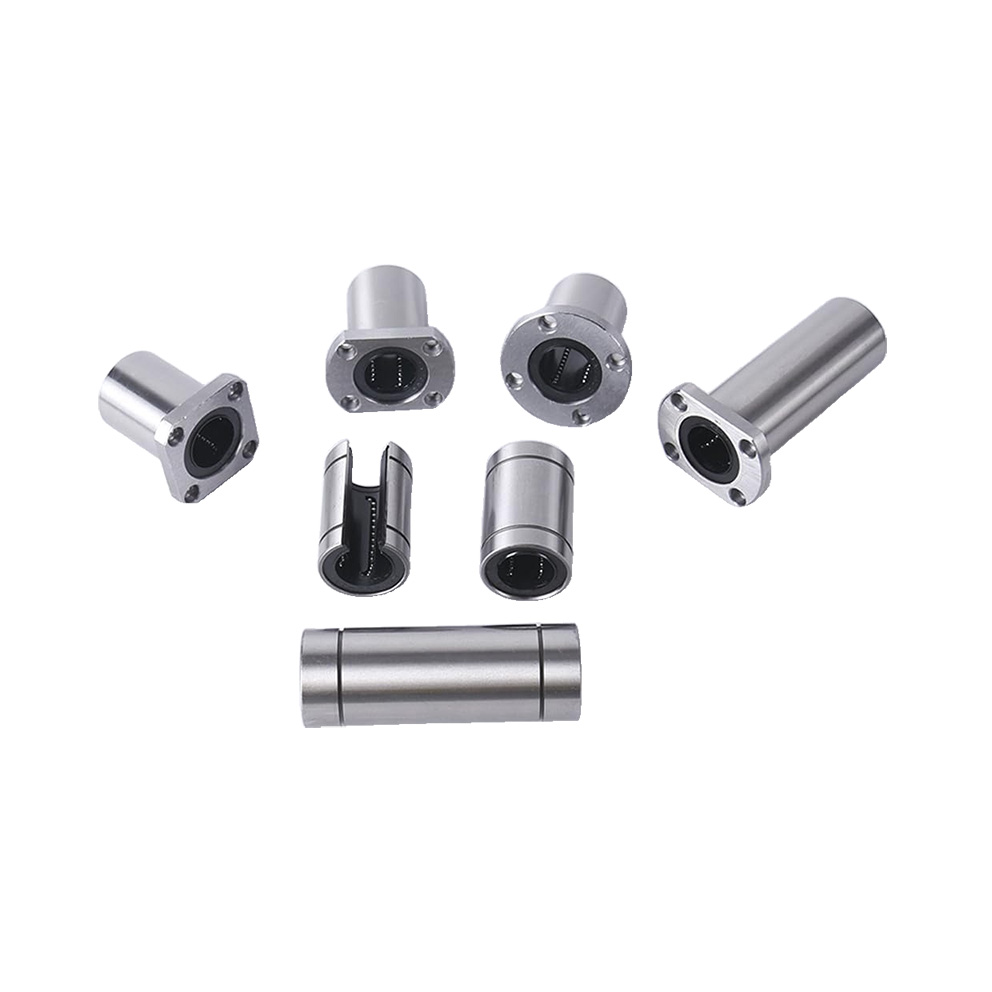
Understand electroplated linear bearings
An electroplated linear bearing is a type of bearing used in linear motion systems, where the bearing moves along a straight path (rather than rotating like traditional bearings). Electroplating refers to the process of coating the bearing’s surface with a thin layer of metal (often nickel or chromium) through an electrochemical process. This coating enhances the performance of the bearing in several ways:
Key features of electroplated linear bearings
- Corrosion Resistance: The electroplated layer, particularly if it’s made of nickel or chromium, protects the bearing against rust and corrosion, making it ideal for use in harsh environments.
- Wear Resistance: The coating improves the surface hardness of the bearing, reducing wear over time, which increases its longevity.
- Friction Reduction: The smoother surface created by electroplating can reduce friction between the bearing and the guide rails, improving the system’s efficiency.
- Aesthetic Appeal: Electroplated bearings have a shiny, polished appearance, which may be important in applications where appearance matters.
- Load Capacity and Precision: The enhanced surface can maintain tight tolerances, which is critical in applications where precise movement is required.
These bearings are commonly used in industries like automotive, aerospace, and automation where smooth and precise linear motion is essential.
Electroplated linear bearings are used in various industries and applications that require precise linear motion and high durability in challenging environments. Some common areas where they are applied include:
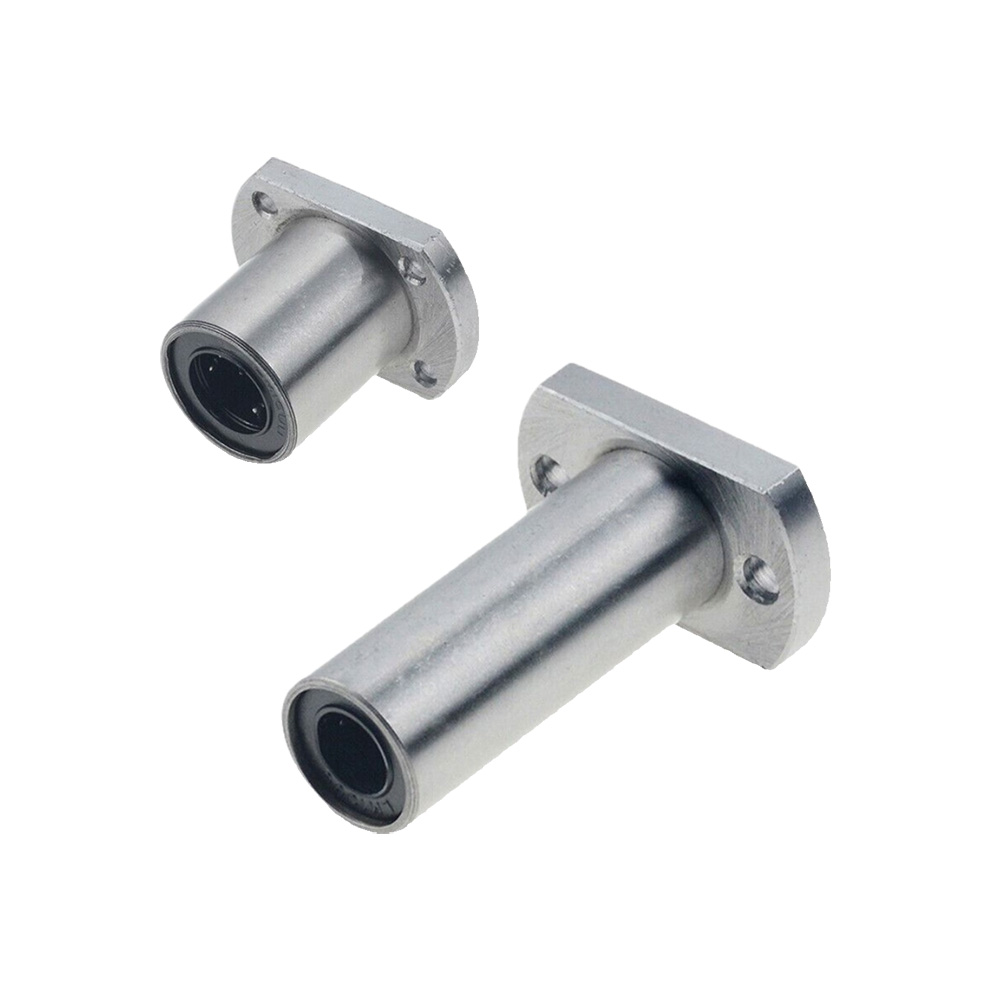
1. Automotive Industry
- Robotics and automation: Used in robotic arms and automated systems for tasks like welding, assembly, and painting.
- Car manufacturing: In assembly lines, for precise movement of parts in automated machinery.
2. Aerospace Industry
- Aircraft components: Used in actuators, control systems, and other areas where precise movement and high durability are needed.
- Satellite systems: In precision instruments or moving parts in space exploration equipment, where corrosion resistance and low friction are critical.
3. Medical Equipment
- Diagnostic machines: For precise motion in imaging systems (MRI, CT scans) or laboratory automation devices.
- Surgical robots: In robotic-assisted surgery, where smooth and precise movement is essential.
4. Packaging and Printing Industries
- Conveyor systems: Electroplated bearings ensure smooth, consistent movement in high-speed packaging lines.
- Printing presses: Used in machines where accurate linear motion is necessary for producing high-quality printed materials.
5. Food and Beverage Industry
- Packaging and bottling lines: In environments where cleanliness, corrosion resistance, and low friction are vital for maintaining hygiene and efficiency.
6. Automation and Industrial Machinery
- CNC machines: In precision manufacturing, such as milling, grinding, and 3D printing, where linear bearings support high-precision, smooth movement.
- Material handling systems: Used in conveyor belts, gantries, and loaders where precise linear movement is required.
7. Marine and Offshore Applications
- Marine equipment: In environments exposed to saltwater or corrosive conditions, electroplated bearings offer durability and protection against rust.
8. Semiconductor Manufacturing
- Precision assembly: In cleanrooms where components must move with high precision and low contamination, the electroplated surface ensures smooth, precise movements.
The corrosion resistance, wear resistance, and precision of electroplated linear bearings make them suitable for industries where both precision and durability are critical, especially in harsh or high-performance environments.
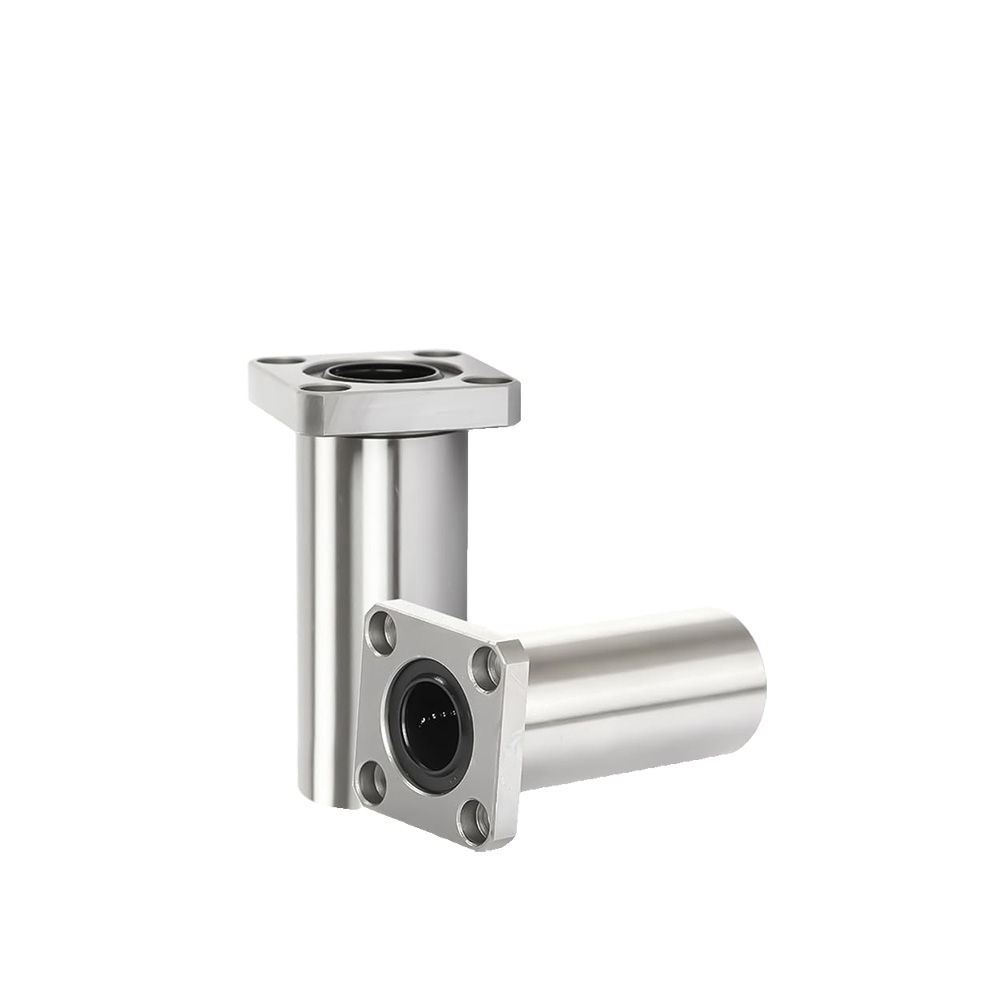
Solution 1: High-Quality Materials Selection
Electroplated linear bearings depend on the selection of high-quality materials to ensure lasting performance. Corrosion-resistant coatings play a pivotal role, especially in environments where moisture or chemicals may be present. Nickel and chromium are frequently chosen for their robust protection against corrosion. Durability of electroplating is also crucial, as it outperforms traditional coatings in maintaining integrity over extended periods. The difference lies in the electrochemical bonding, which provides a tighter adherence. Brands can trust that key metals used in electroplating, like nickel, chromium, and gold, not only offer longevity but are cost-effective by reducing the need for frequent replacements.
Solution 2: Precision Manufacturing Processes
Achieving reliability in electroplated linear bearings hinges on how tight tolerances impact bearing performance. Even slight variations in manufacturing can lead to inefficiencies or increased wear. Utilizing automated machinery in quality control is a cornerstone of modern production processes, ensuring that each bearing meets the precise specifications required. This is vital in large-scale manufacturing where consistency must be maintained across thousands of units. Moreover, precision prevents premature bearing wear, which directly translates into fewer failures and lower costs over time, making it a wise investment for brands aiming for long-term durability.
Solution 3: Consistency in Coating Thickness
Uniformity in electroplating is key to bearing performance. Ensuring even electroplating across surfaces helps to avoid weak points that could result in early failures. If the coating is uneven, it can lead to structural weaknesses or inconsistent load handling. Brands should prioritize thickness uniformity, as it ensures each bearing can manage its intended load capacity without risk of peeling or cracking. Testing methods to confirm coating consistency, such as microscopic inspections and adherence tests, provide further assurance that the bearing will perform reliably under pressure.
Solution 4: Corrosion Resistance in Harsh Environments
Industrial settings often expose bearings to challenging conditions. Common industrial settings requiring corrosion protection include chemical plants, marine environments, and food processing facilities where bearings are frequently exposed to moisture, corrosive chemicals, or salt. How electroplating increases resistance to environmental damage is evident in its ability to form a protective barrier, shielding the underlying metal from corrosive elements. Case studies of electroplated bearings in industries like oil and gas or marine applications demonstrate how they outlast non-plated bearings, ensuring long-term reliability and reducing the need for replacements.
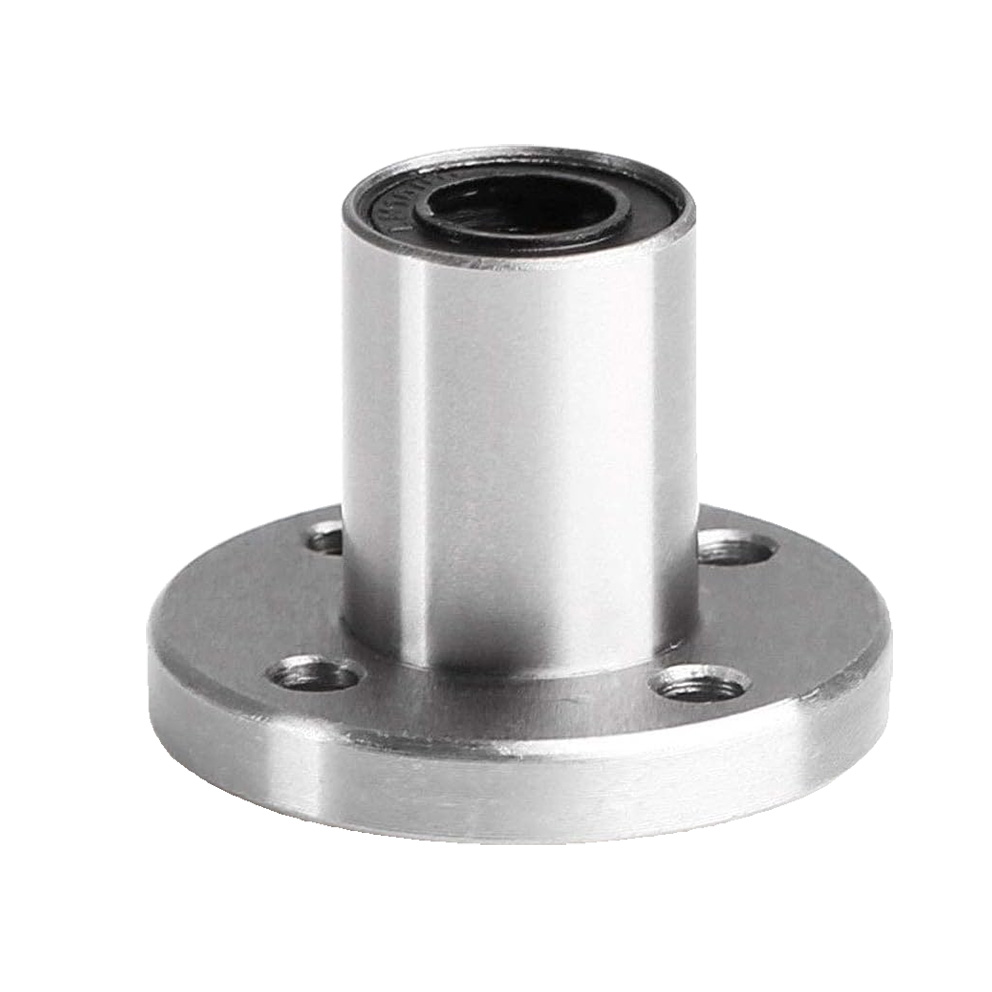
Solution 5: Low Friction for Increased Efficiency
Efficiency is crucial for any machinery, and how electroplated surfaces reduce friction is one of the major advantages for brand procurement professionals. By creating a smooth, low-friction surface, these bearings reduce wear and tear on both the bearings and the equipment they interact with. The effect of reduced friction on energy consumption is another benefit, as machinery operates more smoothly, requiring less energy to achieve the same output. This not only improves performance but also ensures smoother movement in critical applications, such as in high-precision equipment like CNC machines or robotic arms.
Solution 6: Load-Bearing Capacity and Strength
A crucial element of bearing reliability is how electroplated bearings handle heavier loads without compromising performance. The electroplated coating reinforces the structural integrity of the bearing, allowing it to bear greater loads with ease. Why electroplating improves structural integrity lies in the strengthening properties of the plating itself, which adds an extra layer of toughness. Brands should also emphasize testing for strength and load capacity under pressure, ensuring that their bearings can perform under the most demanding conditions without risk of failure, making it a cost-effective choice.
Solution 7: Extended Lifespan for Cost Efficiency
A primary benefit of electroplated bearings is their extended lifespan. Long-term cost benefits come from the reduced need for frequent replacements and the decreased likelihood of machinery breakdown due to bearing failure. By investing in higher-quality electroplated bearings, brands can reduce maintenance through reliable performance, cutting down on both downtime and repair costs. Real-world examples of extended product lifecycles in industries such as aerospace or automotive demonstrate how electroplated bearings continue to perform effectively long after their non-coated counterparts have failed.
Solution 8: Compliance with Industry Standards
For brand procurement professionals, certifications to look for in electroplated bearings can provide peace of mind that the products meet the necessary quality benchmarks. Industry standards, such as ISO certifications, guarantee bearing performance in terms of durability, load-bearing capacity, and corrosion resistance. Regulatory compliance and procurement decisions go hand in hand, as brands need to ensure that the products they purchase are not only reliable but also meet global standards for safety and efficiency.
Solution 9: Versatile Application Across Industries
One of the key strengths of electroplated bearings is their versatility. Industrial automation and electroplated bearings go hand in hand, as their durability and precision are essential for reliable performance in automated systems. How electroplating adapts to varying operational demands is evident in sectors like aerospace, automotive, and even food processing, where each industry has unique requirements. Customization options for specialized industries allow brands to select bearings that are tailored to their specific operational needs, ensuring optimal performance in even the most challenging environments.
Solution 10: Smooth Surface Finish for Reduced Wear
A smooth surface finish is more than just aesthetic; it plays a critical role in reducing wear. The role of smooth finishes in bearing longevity is that they minimize the friction between moving parts, reducing wear and tear over time. How surface finishes minimize wear and tear can be seen in applications where bearings are subjected to continuous motion. Inspection techniques to ensure optimal surface quality, such as visual inspections and surface roughness testing, help guarantee that the bearings will perform reliably over long periods.
Solution 11: Cost-Effective Manufacturing Techniques
Why electroplating is a cost-effective solution is clear: the process enhances durability without significantly increasing production costs. Brands can benefit from reducing manufacturing waste while enhancing quality, as the electroplating process is highly controlled and efficient. Efficiency in mass production without sacrificing reliability is critical for procurement professionals looking for high-quality products at competitive prices, ensuring that the bearings they choose meet both performance and budget requirements.

Solution 12: Quality Assurance and Testing Protocols
Importance of rigorous testing cannot be overstated when it comes to electroplated bearings. Every bearing must undergo common tests to measure performance and durability, such as corrosion resistance testing, load-bearing assessments, and friction evaluations. How quality assurance adds value for procurement professionals is through ensuring that each bearing performs as expected, reducing the risk of costly failures and reinforcing the brand’s reputation for reliability.
Thank you so much for your kind words! We’re glad you found the article helpful and clear. We strive to provide valuable insights on topics like this to support our readers in making informed decisions. Feel free to subscribe to our feed, and we’ll make sure to keep you updated with more content. Your support means a lot to us – we’ll definitely keep the rewarding work going! 🙏