Table of Contents
Categories
-
Adapter Sleeves (9)
-
Ball Bearings (11)
-
Ball Screw Bearings (2)
-
Ceramic Bearings (27)
-
Pillow Block Bearings (4)
-
Plain Bearings (32)
-
Roller Bearings (12)
-
Slewing Bearings (43)
-
Sliding Block (3)
-
Stainless Steel Bearings (27)
-
Super Precision Bearings (6)
-
Thin Section Bearings (9)
-
Track Rollers (4)
-
Universal Joints (1)
Types of Flywheel Bearings: Comparative Analysis and Selection Considerations
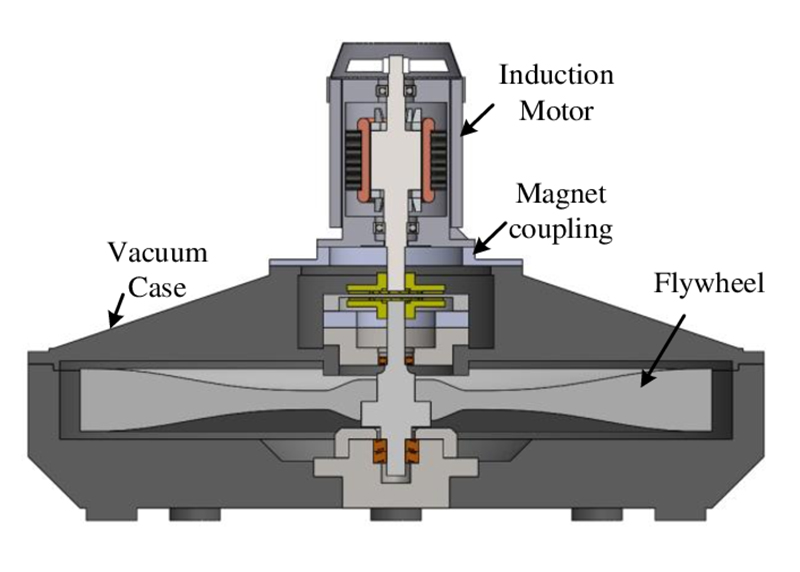
Introduction
Importance of Flywheel Bearings in Mechanical Systems
Flywheel bearings play a pivotal role in the smooth and efficient operation of mechanical systems. Situated at the heart of rotating machinery, these bearings facilitate the transfer of rotational energy, ensuring stability and minimizing frictional losses. By supporting the flywheel’s weight and allowing it to rotate freely, these bearings contribute to maintaining consistent speeds and reducing vibrations, enhancing overall system performance. Whether in automotive engines, industrial machinery, or renewable energy systems, the reliability and durability of flywheel bearings are critical for sustaining operational efficiency and prolonging the lifespan of equipment.
Purpose of Comparative Analysis
The purpose of conducting a comparative analysis of different types of flywheel bearings is to provide engineers and designers with valuable insights into their distinct characteristics and performance attributes. By systematically evaluating factors such as design features, load capacities, and suitability for specific applications, this analysis enables informed decision-making in bearing selection. It helps identify the most suitable bearing type based on the requirements of the mechanical system, balancing considerations such as speed, load capacity, and environmental conditions. Through comparative analysis, engineers can optimize the performance, reliability, and cost-effectiveness of flywheel systems, ultimately enhancing overall efficiency and minimizing maintenance requirements.
Ball Bearings
Ball bearings are a fundamental component of mechanical systems, renowned for their efficiency and versatility. Their design consists of small metal balls housed within inner and outer races, facilitating smooth rotation with minimal friction. This unique arrangement enables ball bearings to efficiently distribute radial and axial loads across the contact surfaces, making them highly effective in supporting various types of rotational motion. Their ability to handle both radial and axial loads is a testament to their versatility, allowing them to accommodate the weight and rotational forces typically encountered in flywheel applications.
In flywheel systems, where rotational stability and efficiency are paramount, ball bearings excel in providing reliable performance. Their capability to support the weight of the flywheel while ensuring smooth rotation is crucial for maintaining the overall functionality of the system. Additionally, ball bearings offer high-speed capabilities, allowing flywheels to achieve rapid acceleration and deceleration without compromising performance. This characteristic is particularly beneficial in applications where dynamic response and precision are essential, such as automotive engines and industrial machinery.
Moreover, the compact size and lightweight design of ball bearings contribute to the overall efficiency of flywheel systems. By minimizing energy losses and maximizing output, ball bearings help optimize the performance and reliability of flywheel applications across various industries. Whether in automotive engines, power generation equipment, or renewable energy systems, the versatility and efficiency of ball bearings make them indispensable components in flywheel technology.
Roller Bearings
Roller bearings represent another crucial category of bearings widely utilized in various mechanical systems, including flywheel applications. They feature cylindrical, tapered, or spherical rollers arranged between inner and outer races, enabling efficient load distribution and smooth rotation. The cylindrical roller variant offers high radial load capacity, making it suitable for applications with heavy radial loads, such as flywheel systems requiring robust support. Tapered roller bearings, characterized by tapered roller elements, are designed to handle both radial and axial loads, providing versatility and reliability in flywheel applications where dynamic forces are prevalent. Spherical roller bearings feature barrel-shaped rollers, allowing them to accommodate misalignment and axial displacement, ideal for flywheels operating under variable conditions.
In terms of load capacities and performance, roller bearings offer distinct advantages over other types of bearings. Their larger contact area and increased number of rolling elements result in enhanced load-bearing capabilities, making them well-suited for demanding flywheel applications. Additionally, roller bearings exhibit lower friction compared to ball bearings, reducing energy losses and contributing to improved efficiency in flywheel systems. Their ability to operate at higher speeds while maintaining stability further enhances their suitability for flywheel applications requiring precision and reliability.
When considering the suitability of roller bearings for flywheel applications, their design variants and performance characteristics play a critical role. The choice between cylindrical, tapered, or spherical roller bearings depends on factors such as the magnitude and direction of applied loads, operating speeds, and environmental conditions. For flywheel systems requiring high radial load capacity, cylindrical roller bearings are preferred, while tapered roller bearings offer versatility in handling both radial and axial loads. Spherical roller bearings, on the other hand, provide flexibility to accommodate misalignment and axial displacement, making them suitable for flywheels operating under variable conditions.
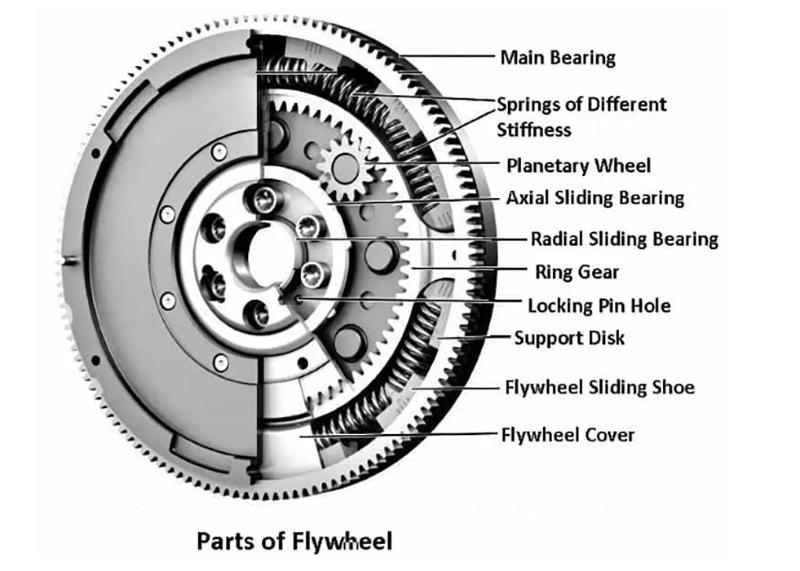
Plain Bearings
Plain bearings, also referred to as bushings or sleeve bearings, are fundamental components within mechanical systems, valued for their straightforward design and operational reliability. Unlike rolling-element bearings, plain bearings feature a smooth cylindrical surface, typically crafted from materials like bronze, brass, or polymer for optimal friction reduction and wear resistance. Operating on the principle of hydrodynamic lubrication, a thin film of lubricant separates the shaft from the bearing surface, mitigating friction and wear. This mechanism enables plain bearings to efficiently support heavy loads and deliver smooth, low-friction motion in flywheel applications.
In terms of load capacities and performance, plain bearings offer distinct advantages suitable for flywheel applications. Their simple yet robust design enables them to endure significant radial and axial loads while ensuring smooth rotation. Moreover, plain bearings exhibit minimal friction and wear, leading to decreased energy losses and prolonged service life in flywheel systems. Their self-lubricating nature eliminates the need for additional lubrication systems, simplifying maintenance and reducing operational costs.
When assessing plain bearings’ suitability for flywheel applications, various factors must be considered. Bearing material selection, such as bronze, brass, or polymer, depends on load intensity, operational speed, and environmental conditions. Additionally, precise shaft alignment and surface finish are essential to optimize performance and longevity. While plain bearings may lack the high-speed capabilities and precision of rolling-element bearings, their reliability and load-bearing capacity make them well-suited for flywheel applications across diverse industries.
Hybrid Bearings
Hybrid bearings represent an innovative fusion of different bearing technologies, combining the strengths of various designs to optimize performance in specific applications such as flywheels. These bearings integrate elements from both rolling-element and plain bearing designs, leveraging the advantages of each to achieve superior load capacities and performance characteristics. By combining features like the low friction and high-speed capabilities of ball or roller bearings with the robustness and load-bearing capacity of plain bearings, hybrid bearings offer enhanced efficiency and reliability in flywheel applications.
In terms of load capacities and performance, hybrid bearings exhibit remarkable capabilities owing to their composite design. They can efficiently handle both radial and axial loads, providing stability and smooth operation in flywheel systems subject to varying forces and speeds. The integration of different bearing technologies allows hybrid bearings to distribute loads effectively, reducing friction and minimizing energy losses while maximizing load-bearing capacity. This results in improved overall performance and longevity of flywheel systems.
The suitability of hybrid bearings for flywheel applications lies in their ability to offer tailored solutions to specific requirements. Their customizable design allows engineers to optimize performance based on factors such as load intensity, operating speed, and environmental conditions. Whether it’s achieving high-speed operation, minimizing friction, or enhancing load-bearing capacity, hybrid bearings offer versatility and adaptability to meet the diverse needs of flywheel applications across industries.
Comparative Analysis of Bearing Types
Performance Metrics Comparison
Various metrics, including friction, speed capability, and durability, are compared to assess the suitability of different bearing types for specific applications. Friction, a significant factor affecting efficiency and energy consumption, is closely examined to determine the bearing’s contribution to overall system losses. Speed capability indicates the maximum rotational speed at which a bearing can operate reliably without compromising performance or longevity. Durability metrics such as fatigue life and wear resistance provide insights into the bearing’s ability to withstand repetitive loading and harsh operating conditions. By comparing these performance metrics across different bearing types, engineers can identify the most suitable option that aligns with the requirements of the application, ultimately optimizing system performance and reliability.
Cost Analysis
In addition to performance metrics, conducting a cost analysis is essential in comparing different bearing types for optimal selection. Cost considerations encompass both initial investment and long-term maintenance expenses. Initial costs involve the purchase price of the bearing components, which vary depending on factors such as material quality, manufacturing complexity, and brand reputation. However, long-term maintenance costs, including lubrication requirements, replacement intervals, and potential downtime, are equally significant. Bearings requiring frequent maintenance or replacement may incur higher operational expenses over their lifespan. By analyzing both upfront costs and ongoing maintenance expenses, engineers can make informed decisions that balance performance requirements with budgetary constraints, ultimately optimizing the overall cost-effectiveness of the bearing selection for the specific application.
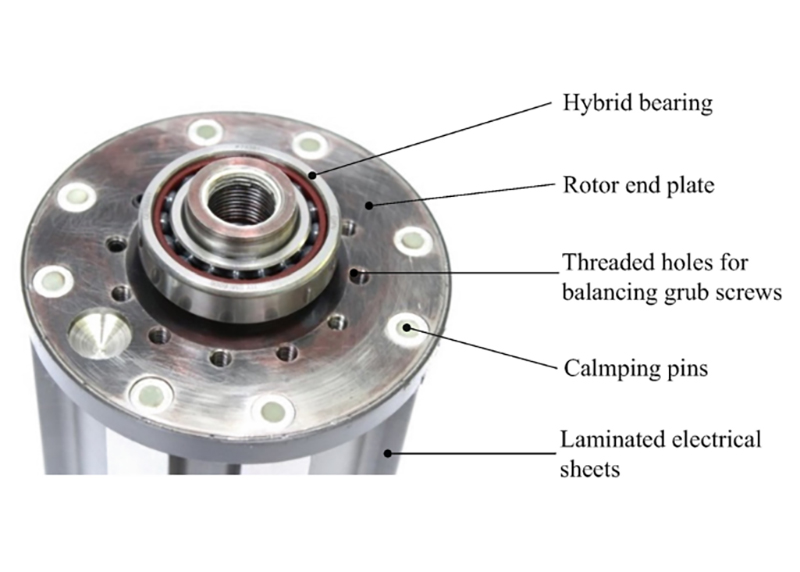
Selection Considerations for Flywheel Bearings
When selecting flywheel bearings, several key considerations must be taken into account to ensure optimal performance and reliability. Firstly, the operating conditions of the flywheel system play a crucial role. Factors such as rotational speed, temperature variations, and shock loads dictate the bearing’s requirements in terms of material selection, lubrication, and design features. Secondly, understanding the load requirements is essential to determine the bearing’s load capacity and suitability for the application. This includes considering both radial and axial loads, as well as dynamic forces that may arise during operation. Additionally, environmental factors such as exposure to contaminants, humidity levels, and corrosion potential must be evaluated to choose bearings with appropriate protective measures and materials.
Furthermore, maintenance considerations are paramount in ensuring prolonged bearing lifespan and minimizing downtime. Assessing lubrication requirements, accessibility for maintenance tasks, and potential replacement intervals helps determine the bearing’s overall maintenance needs and associated costs. By carefully evaluating these selection considerations, engineers can identify the most suitable flywheel bearings that meet the operational demands, environmental conditions, and maintenance requirements of the specific application, ultimately maximizing system performance and reliability while minimizing lifecycle costs.
Challenges and Limitations
Despite their numerous advantages, flywheel bearings are subject to certain challenges and limitations that warrant consideration during selection and design. Heat dissipation is a critical issue, particularly in high-speed or heavy-load applications, as excessive heat can lead to premature wear and failure of bearing components. Adequate heat management strategies, such as proper lubrication, cooling systems, and bearing material selection, are essential to mitigate this challenge effectively. Additionally, noise and vibration can pose significant challenges, especially in precision applications where smooth operation is paramount. Minimizing noise and vibration requires careful design considerations, such as optimizing bearing geometry, surface finishes, and damping mechanisms, to reduce unwanted resonances and disturbances.
Moreover, compatibility with advanced materials presents another limitation for flywheel bearings. While advancements in materials science offer opportunities for improved performance and durability, integrating new materials into bearing designs may introduce compatibility issues or require additional testing and validation. Ensuring compatibility between bearing materials and other system components is crucial to prevent adverse effects such as premature wear, corrosion, or material degradation. Addressing these challenges and limitations requires a holistic approach that considers various factors, including operating conditions, load requirements, environmental factors, and maintenance considerations, to optimize the performance and reliability of flywheel bearings in diverse applications.
Conclusion
In conclusion, flywheel bearings are indispensable components in mechanical systems, ensuring smooth operation, stability, and efficiency. Through comparative analysis, engineers can choose from ball bearings, roller bearings, plain bearings, and hybrid bearings, considering factors like load capacity, speed capability, and cost-effectiveness. Selection considerations must account for operating conditions, load requirements, and maintenance needs to optimize performance and reliability. Despite challenges such as heat dissipation and compatibility with advanced materials, strategic design and maintenance strategies can mitigate risks. By leveraging insights from this analysis, engineers can make informed decisions to enhance the performance, longevity, and cost-effectiveness of flywheel systems across diverse industries.
References
- 1.”Bearings for Flywheel Energy Storage” from SPRINGER LINK;
- 2. “Flywheel/Bearings” from CleverIR;
- 3. “Flywheel” from Wikipedia.