Table of Contents
Categories
Spin It Right: Elevate Performance with Expert Bearing Cages
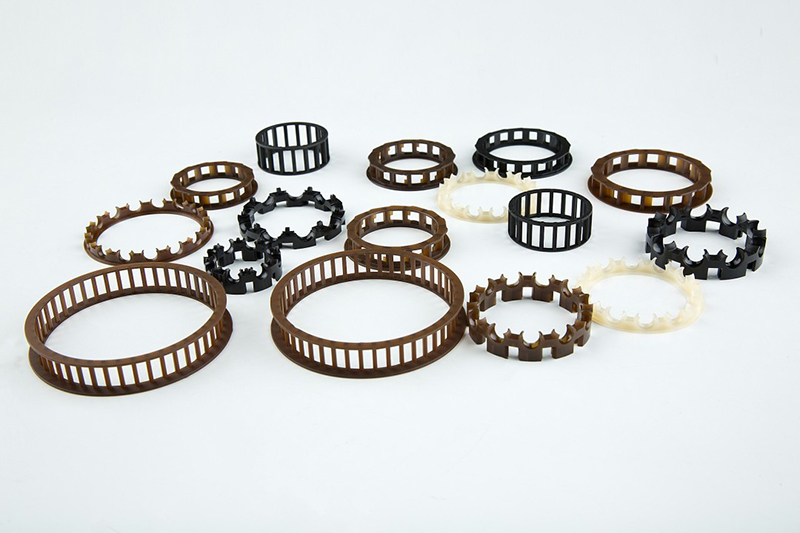
Introduction
Definition of Bearing Cages
Bearing cages, also known as bearing retainers or bearing separators, are integral components in the realm of mechanical systems. These devices serve a crucial role by providing structural support and organization to the rolling elements within a bearing. Often constructed from materials like steel, brass, or plastic, bearing cages facilitate the efficient functioning of various types of bearings by preventing direct contact between rolling elements, mitigating friction, and maintaining proper spacing.
Importance of Bearing Cages in Mechanical Systems
The significance of bearing cages cannot be overstated in the broader context of mechanical engineering. These unassuming components contribute fundamentally to the stability, longevity, and overall efficiency of mechanical systems. By ensuring the proper alignment and separation of rolling elements, bearing cages play a pivotal role in minimizing friction, reducing wear and tear, and promoting the smooth operation of bearings across diverse applications.
Overview of the Role of Bearing Cages in Bearings
Understanding the multifaceted role of bearing cages within different types of bearings is essential for engineers and professionals in the field. Bearing cages act as guardians, preventing the entanglement and misalignment of rolling elements, thereby preserving the integrity of the entire bearing assembly. Their influence extends beyond mere structural support, as they actively contribute to the overall performance and reliability of various bearing configurations.
Types of Bearings
Brief Introduction to Different Types of Bearings
Bearings, crucial components in machinery, facilitate smooth motion by reducing friction between moving parts. Diverse types cater to specific needs, each playing a unique role in various applications. Ball bearings, featuring small metal balls, excel in radial and thrust loads. Roller bearings, utilizing cylindrical or tapered rollers, offer enhanced load distribution. Needle bearings, compact yet robust, excel in constrained spaces. Thrust bearings manage axial loads, ideal for applications demanding force control. Spherical bearings accommodate misalignment, vital in complex systems. Understanding these variations is key to optimizing performance across industries, from automotive to industrial machinery, ensuring efficiency and longevity in dynamic mechanical operations.
Significance of Bearing Cages in Different Bearing Designs
- Friction Reduction: Bearing cages in ball bearings maintain proper spacing of balls, minimizing friction and promoting smooth rotation.
- Load Distribution: They ensure even distribution of loads, preventing ball-to-ball contact and enhancing overall durability.
- Load Stability: Bearing cages in roller bearings support roller alignment, preventing skewing and maintaining stability under heavy loads.
- Enhanced Lubrication: Cages facilitate efficient lubricant distribution, reducing wear and heat buildup in high-load situations.
Needle Bearings:
- Space Optimization: Bearing cages in needle bearings guide needle rollers, enabling compact designs without sacrificing load-bearing capacity.
- Shock Absorption: They contribute to shock absorption by preventing direct contact between needle rollers.
Thrust Bearings:
- Axial Load Management: Bearing cages maintain proper spacing, preventing axial loads from causing direct contact between rolling elements and ensuring efficient load distribution.
- Precision Control: They play a crucial role in maintaining precision and alignment under thrust loads.
Spherical Bearings:
- Misalignment Compensation: Bearing cages allow controlled movement, accommodating misalignment and preventing excessive stress on rolling elements.
- Versatile Performance: They contribute to the adaptability of spherical bearings in applications with varying degrees of shaft misalignment.
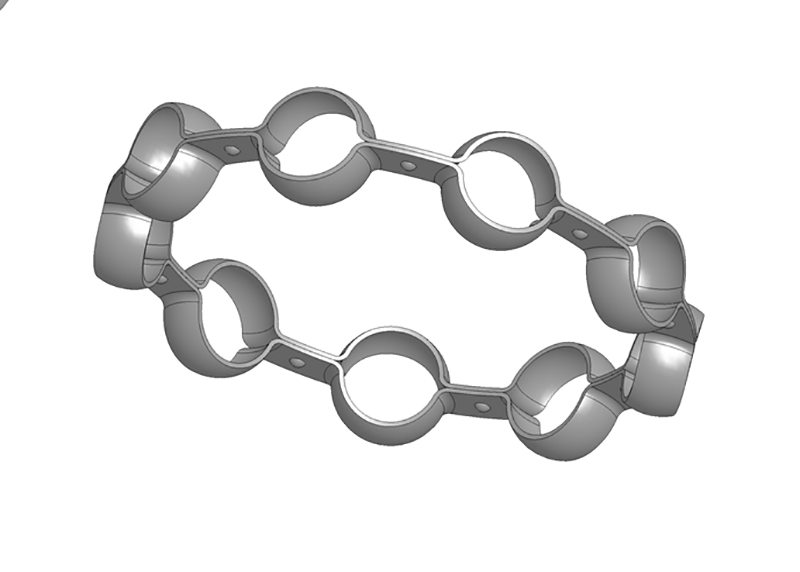
Functions of Bearing Cages
Retaining and Separating Rolling Elements
The bearing cage, a critical component, plays a pivotal role in retaining and separating rolling elements within a bearing. By precisely spacing elements such as balls, rollers, or needles, the cage prevents direct contact, ensuring optimal load distribution. This not only reduces friction, promoting smooth rotation, but also enhances the bearing’s durability by preventing wear and localized stress. Additionally, in compact designs like needle bearings, the cage guides and separates rollers, enabling efficient load-bearing in constrained spaces while maintaining structural integrity.
Reducing Friction and Wear
Bearing cages play a pivotal role in minimizing friction and wear within bearings. By ensuring optimal spacing and alignment of rolling elements, such as balls or rollers, cages prevent direct contact during rotation. This separation reduces friction, preserving the bearing’s integrity and promoting smooth operation. The cage acts as a protective barrier, mitigating wear on critical components. This dual function not only extends the lifespan of the bearing but also enhances overall machinery reliability. In essence, bearing cages are indispensable in maintaining low-friction environments, reducing wear, and optimizing the performance and longevity of mechanical systems.
Heat Dissipation in Bearings
The heat dissipation function of bearing cages and bearings is crucial for maintaining optimal operating conditions. Bearing cages, by preventing direct contact between rolling elements, reduce frictional heat generation during rotation. Simultaneously, the bearing itself acts as a heat sink, absorbing and dispersing generated heat. This dual mechanism ensures effective heat dissipation, preventing overheating that could compromise performance and longevity. Efficient heat management is essential in industrial applications, enhancing the overall reliability of machinery and promoting sustained operational efficiency. In essence, bearing cages and bearings collaborate to create a thermal equilibrium, contributing to the longevity and reliability of mechanical systems.
Materials Used in Bearing Cages
Common Cage Materials
Steel: Often made from high-carbon or stainless steel, steel cages provide durability and resistance to corrosion.
Brass: Brass cages offer good wear resistance, high strength, and corrosion resistance, making them suitable for various applications.
Nylon: Nylon cages are lightweight, have good wear resistance, and are effective in damp or corrosive environments.
Polymer/Plastic: Polymer or plastic cages provide corrosion resistance, low friction, and can be suitable for applications with specific environmental requirements.
Bronze: Bronze cages offer high strength, durability, and resistance to wear and corrosion, making them suitable for heavy-duty applications.
Machined Steel: Precision-machined steel cages are used for high-performance applications where tight tolerances are essential.
Factors Influencing Cage Material Selection
The selection of cage materials for bearings is influenced by several critical factors. Firstly, the operational environment plays a key role; corrosive atmospheres may favor corrosion-resistant materials like stainless steel or certain polymers. The load and speed conditions impact material strength requirements, with brass or steel suitable for heavy loads. Temperature considerations may drive the choice towards materials with high-temperature resistance, such as specialized polymers. Additionally, factors like lubrication compatibility, cost, and manufacturing processes contribute to the decision. Each material, whether steel, brass, nylon, polymer, or bronze, brings unique properties that must align with the specific demands of the application, emphasizing the importance of a tailored approach to cage material selection.
Cage Designs
Standard Cage Designs
Among various bearing cage designs, the standard features a classic, ball-guided structure. This design employs a circular or polygonal framework with strategically placed openings to secure and guide rolling elements, such as balls or rollers. The ball-guided design allows for smooth rotation while maintaining proper spacing and alignment. This standard cage design is versatile, providing stability under varying loads and speeds. Its simplicity and effectiveness make it a prevalent choice across industries. However, specific applications may call for alternative designs like window-type, ribbon-type, or pocket-type cages, each tailored to address unique performance requirements and environmental conditions.
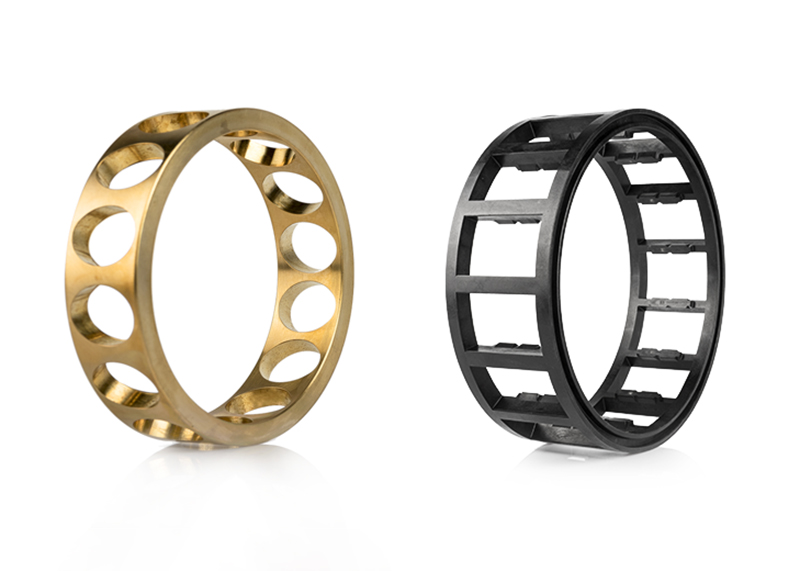
Customized Cage Designs for Specific Applications
In addition to standard designs, specialized cage designs cater to unique application requirements in bearing technology. The ribbon-type cage, with its continuous ribbon-like structure, ensures optimal lubrication efficiency, reducing friction and wear, making it ideal for high-speed applications. The window-type cage, characterized by interconnected openings, offers enhanced guidance to rolling elements and facilitates efficient lubrication. Pocket-type cages, featuring individual pockets for each rolling element, provide exceptional stability and load distribution, making them suitable for heavy-duty scenarios. Customized cage designs go beyond the conventional, showcasing the versatility of bearings in addressing diverse industrial challenges by tailoring cage structures to specific operational demands, ultimately optimizing performance and longevity in various applications.
Cage Selection Criteria
Factors Influencing Cage Selection
Several critical factors influence the selection of bearing cages, emphasizing the importance of tailored choices. Environmental conditions, including temperature, humidity, and corrosive elements, guide the selection toward materials with appropriate resistance. Load and speed considerations impact cage strength and design, with heavy loads often requiring robust materials like steel or bronze. Lubrication compatibility influences the choice, favoring materials that work well with specific lubricants. Cost considerations, manufacturing processes, and industry standards also play pivotal roles. The diverse array of cage designs, from standard ball-guided structures to specialized ribbon or pocket types, provides flexibility to address unique challenges. A comprehensive understanding of these factors ensures the optimal selection of bearing cages, contributing to reliable and efficient machinery performance.
Matching Cages to Specific Applications
To match bearing cages with specific applications, engineers must conduct a comprehensive assessment. Consider environmental factors such as temperature, humidity, and corrosiveness, guiding the selection toward materials with suitable resistance. Evaluate load conditions, opting for robust materials like steel for heavy loads. High-speed applications benefit from designs promoting efficient lubrication. Customized applications may require specialized cage designs like ribbon or pocket types. Assess lubrication compatibility to ensure sustained performance. Factor in cost considerations, manufacturing processes, and industry standards. The goal is a meticulous alignment of cage material and design with the unique demands of the application, optimizing load distribution, friction reduction, and overall efficiency. This tailored approach ensures seamless operation within the intended environment, enhancing reliability and performance over time.
Compatibility with Bearing Types
Ensuring compatibility between bearing cages and various bearing types involves a meticulous understanding of each type’s unique requirements. For ball bearings, choose cages that enable smooth ball movement, ensuring even load distribution. Roller bearings demand cages that support and guide rollers effectively, maintaining stability under varying loads. Needle roller bearings, with their compact design, require cages that optimize space and facilitate precise needle roller movement. Assess the specific load, speed, and alignment characteristics of each bearing type. Consider factors like lubrication needs and environmental conditions. By tailoring cage materials and designs to harmonize with the distinct attributes of ball, roller, or needle roller bearings, engineers ensure seamless integration, maximizing the overall efficiency and longevity of the bearing system.
Conclusion
In conclusion, bearing cages play a pivotal role in the stability, longevity, and efficiency of mechanical systems. Serving as guardians for rolling elements in various types of bearings, these devices ensure optimal load distribution, reduce friction, and contribute to heat dissipation. The choice of cage material and design is influenced by factors such as environmental conditions, load requirements, and lubrication compatibility. Standard and customized cage designs offer versatility to address specific application demands. Engineers must meticulously match cages to different bearing types, considering their unique characteristics. A tailored approach to cage selection enhances machinery reliability, efficiency, and overall performance in diverse industrial settings.
References
1.”Cages (Retainers and Separators)” from New Hampshire Ball Bearings;
2. “Common Ball Bearing Cages” from Bearing News;
3. “Bearing Cages” from SKF.
Related Posts
sensor bearings
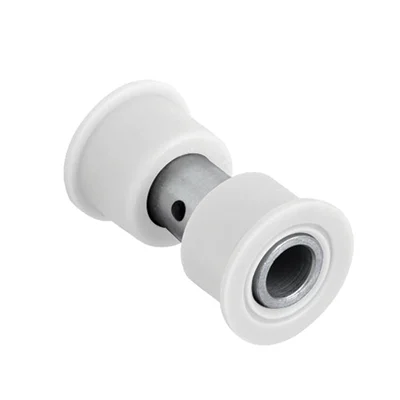
Delrin Bearings: Lubrication-Free Long Life
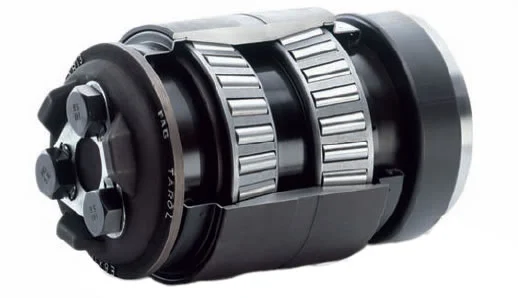
Locomotive Bearing Specs That Matter Most
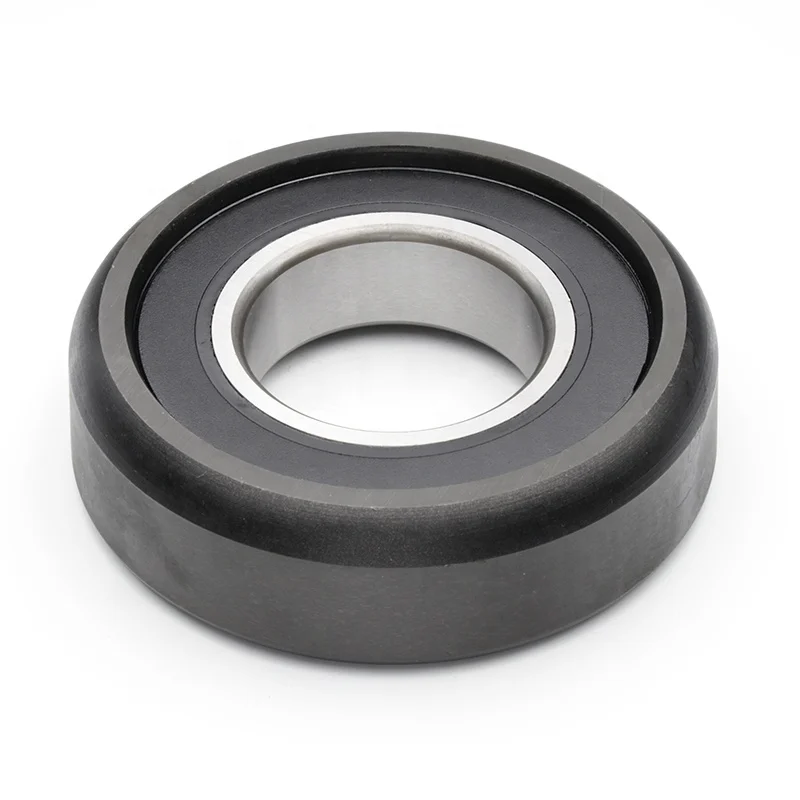